Advancements in Double Girder Overhead Crane Load Monitoring Systems
- blog@ellsenbridgecrane.com
- Jul 11, 2024
- 4 min read
Double girder overhead cranes are integral to modern industrial operations, providing the strength and reliability needed for heavy lifting and precise material handling. Among the most significant advancements in this field is the evolution of load monitoring systems. These systems enhance safety, efficiency, and reliability, addressing critical concerns in industries ranging from manufacturing to shipping and construction. This article explores the latest advancements in double girder overhead crane load monitoring systems, highlighting their benefits and the technological innovations driving these improvements.
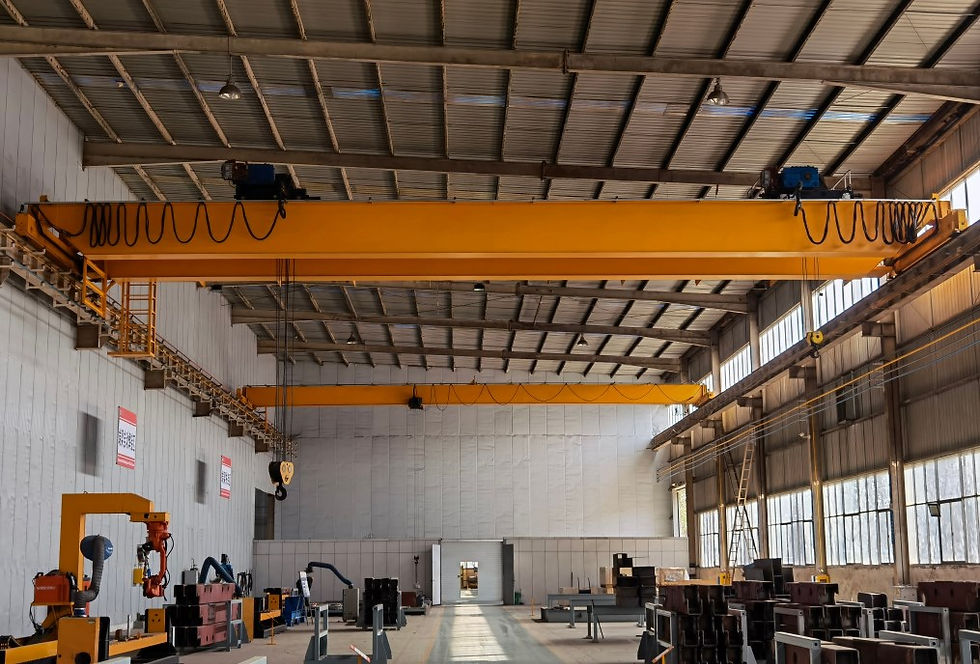
The Importance of Load Monitoring Systems
Load monitoring systems are crucial for the safe operation of Aicrane double girder overhead cranes. They provide real-time data on the weight and distribution of loads, ensuring that cranes operate within their safe working limits. By preventing overloading and uneven load distribution, these systems mitigate the risk of mechanical failures, accidents, and equipment damage. This not only protects workers but also extends the lifespan of the crane and minimizes downtime, thus improving overall operational efficiency.
Technological Advancements in Load Monitoring Systems
1. Digital Load Cells
Traditional analog load cells have been largely replaced by digital load cells in modern load monitoring systems. Digital load cells offer higher accuracy, better stability, and improved signal transmission. They convert the mechanical force exerted by the load into an electrical signal, which is then processed and displayed in real time. These cells are less susceptible to signal interference and degradation over long distances, ensuring precise load measurements.
2. Wireless Communication
Wireless communication has revolutionized load monitoring in double girder overhead cranes. Wireless load cells and transmitters eliminate the need for cumbersome and vulnerable wiring, reducing maintenance costs and improving system reliability. These wireless systems use radio frequency (RF) technology to transmit load data to the crane’s control system or a remote monitoring station. This allows for greater flexibility in crane operations and enables real-time monitoring from any location within the facility.
3. Integrated Data Analytics
Modern load monitoring systems are equipped with advanced data analytics capabilities. These systems collect and analyze data from multiple sensors, providing insights into load patterns, usage trends, and potential issues. Predictive analytics can forecast maintenance needs and identify abnormal load conditions before they lead to equipment failure. This proactive approach enhances operational efficiency and reduces unexpected downtime.
4. Internet of Things (IoT) Integration
The integration of IoT technology has further advanced load monitoring systems. IoT-enabled load cells and sensors can communicate with each other and with central management systems over the internet. This connectivity allows for seamless data sharing and remote monitoring, enabling operators to track crane performance and load conditions in real time from any location. IoT integration also facilitates the implementation of smart maintenance programs, where maintenance activities are scheduled based on actual usage and load data rather than predefined intervals.
5. Advanced User Interfaces
The user interfaces of load monitoring systems have become more sophisticated and user-friendly. Touchscreen displays, graphical dashboards, and intuitive software provide operators with a comprehensive view of crane operations. These interfaces offer real-time load data, historical trends, and diagnostic information, helping operators make informed decisions quickly. The ease of use of these interfaces reduces the learning curve for new operators and improves overall productivity. Learn more: https://steelmillcranes.com/
Benefits of Modern Load Monitoring Systems
1. Enhanced Safety
The primary benefit of advanced load monitoring systems is enhanced safety. By providing accurate and real-time load data, these systems help prevent overloading and uneven load distribution, which are major causes of crane accidents. Safety alarms and automatic shutdown features can be integrated into the system to halt crane operations if unsafe conditions are detected, further reducing the risk of accidents.
2. Improved Efficiency
Modern load monitoring systems improve operational efficiency by optimizing crane performance. Accurate load data allows operators to manage lifts more effectively, reducing cycle times and increasing throughput. The predictive maintenance capabilities of these systems also minimize downtime, ensuring that cranes are available when needed and reducing the impact of maintenance activities on production schedules.
3. Cost Savings
By preventing overloading and reducing wear and tear on crane components, load monitoring systems contribute to significant cost savings. They extend the lifespan of the crane and its components, reducing the frequency and cost of repairs and replacements. Additionally, the efficiency gains achieved through better load management and reduced downtime translate into lower operational costs.
4. Compliance with Regulations
Many industries are subject to strict safety regulations regarding crane operations. Advanced load monitoring systems help companies comply with these regulations by providing accurate documentation of load handling activities. This documentation can be used to demonstrate compliance during audits and inspections, avoiding potential fines and legal issues.
Case Study: Implementation in Heavy Manufacturing
In the heavy manufacturing industry, the implementation of advanced load monitoring systems in double girder overhead cranes has led to remarkable improvements. For instance, a steel manufacturing plant integrated wireless load cells and IoT-enabled sensors into their crane operations. The real-time data and predictive analytics allowed for better load management and maintenance scheduling. As a result, the plant saw a 20% reduction in downtime and a 15% increase in production efficiency. Moreover, the enhanced safety features helped achieve a significant reduction in workplace accidents, improving overall worker safety.
Future Trends
Looking ahead, the future of load monitoring systems in double girder overhead cranes is promising. Emerging technologies such as artificial intelligence (AI) and machine learning (ML) are expected to play a significant role in further advancing these systems. AI and ML can enhance predictive maintenance capabilities, optimize load management algorithms, and provide even more accurate real-time data analysis. Additionally, the continued development of IoT technology will lead to greater connectivity and integration, enabling even more sophisticated and efficient crane operations.
Conclusion
The advancements in double girder overhead crane load monitoring systems have revolutionized the field, bringing unprecedented levels of safety, efficiency, and reliability. From digital load cells and wireless communication to IoT integration and advanced data analytics, these innovations are transforming how cranes are operated and maintained. As technology continues to evolve, we can expect even greater advancements that will further enhance the capabilities and benefits of load monitoring systems in industrial applications. The commitment to leveraging these technologies ensures a safer, more efficient, and cost-effective future for crane operations across various industries.
Comments