Cost Considerations: How to Budget for an Overhead Crane in Your Factory
- blog@ellsenbridgecrane.com
- Oct 14, 2024
- 4 min read
Installing an overhead crane in a factory is a critical investment that enhances productivity, efficiency, and safety in material handling. Overhead cranes are widely used in industries such as manufacturing, construction, automotive, and metalworking, where heavy materials need to be moved quickly and safely. However, purchasing and installing an overhead crane involves a significant financial outlay, and it’s essential to carefully consider all cost factors to ensure a sound investment. This article will outline the key cost considerations to help you effectively budget for a factory overhead crane.

1. Types of Overhead Cranes and Their Price Range
Overhead cranes come in various types, each with different price points depending on their complexity and application. The primary types include:
Single Girder Overhead Cranes: These cranes are typically used for lighter loads (up to 20 tons). They have a simpler structure, which makes them less expensive to purchase and install compared to double girder cranes. Their cost ranges from $10,000 to $50,000, depending on capacity, span, and lifting height.
Double Girder Overhead Cranes: Designed for heavier lifting (over 20 tons), double girder cranes are more robust and have higher load capacities. They are ideal for applications where the crane will be in frequent use, lifting heavier loads. Double girder cranes are more expensive, with costs ranging from $50,000 to $200,000 or more.
Underslung Cranes: These are installed underneath existing beams or ceiling structures, making them suitable for facilities with space constraints. Depending on specifications, they may cost between $15,000 and $75,000.
Top-Running Cranes: Installed on a runway system mounted on top of the building columns, Aicrane top running cranes are versatile and can handle larger loads. Their prices are generally higher due to the structural requirements for the runway system, ranging from $50,000 to $250,000.
2. Crane Capacity and Its Impact on Cost
The load capacity of the crane significantly impacts the overall cost. Overhead cranes are available in a wide range of capacities, from 1 ton to over 100 tons. Larger capacity cranes require more robust construction, heavier-duty components, and a more powerful motor, all of which contribute to a higher price tag.
Light-Duty Cranes: For capacities under 10 tons, you can expect costs to be on the lower end of the spectrum. These cranes are ideal for lighter materials and infrequent use. Budget approximately $10,000 to $30,000 for a light-duty crane.
Medium-Duty Cranes: Cranes with capacities between 10 and 50 tons are suitable for moderate use in factories. The cost typically ranges from $30,000 to $100,000, depending on the specific features and customization.
Heavy-Duty Cranes: Cranes over 50 tons, designed for continuous use in heavy industrial settings, come with a higher price. Expect to budget $100,000 to $300,000 or more for these cranes, especially if customization or automation features are required.
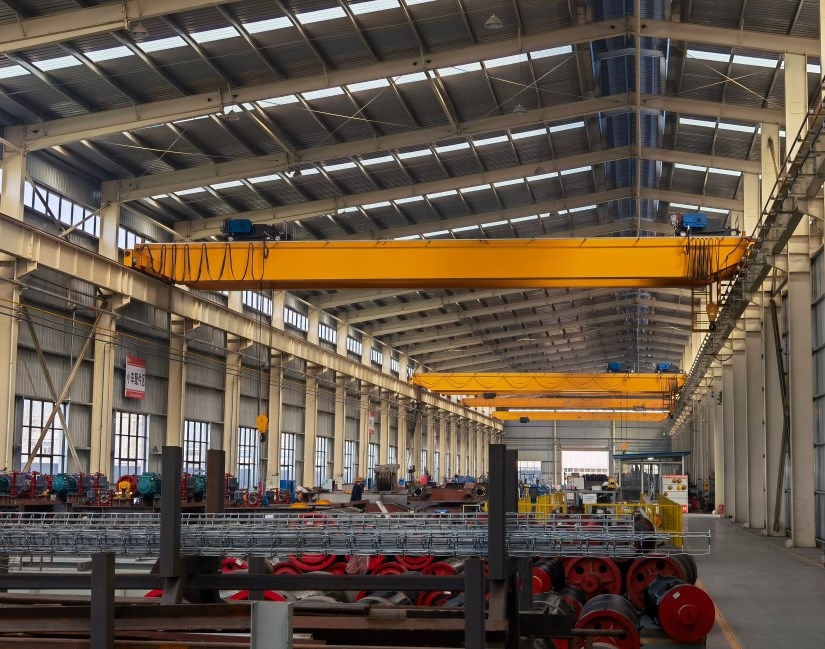
3. Installation Costs
The cost of installing an overhead crane depends on several factors, including the complexity of the installation, the need for any structural modifications to the factory, and the location of the facility.
Runway Installation: Most overhead cranes require a runway system, either top-running or underslung. Installing a runway system may involve significant construction work, particularly if your factory needs additional structural support. Runway installation costs can range from $10,000 to $50,000, depending on the size of the crane and the condition of your factory structure.
Factory Modifications: In some cases, the factory’s roof or columns may need to be reinforced to support the crane. Structural modifications may add anywhere from $5,000 to $50,000 to the total cost.
Labor and Installation Time: Installation labor costs will vary depending on the complexity of the crane and the region where your factory is located. The installation process typically requires skilled labor, and costs can range from $5,000 to $30,000.
4. Electrical and Control Systems
The electrical and control systems of an overhead crane are critical components that ensure smooth, safe, and efficient operation. The cost of these systems depends on whether you opt for a basic setup or advanced features such as automation, remote control, or anti-sway technology.
Basic Control Systems: For standard operations, basic electrical and control systems will cost between $5,000 and $20,000.
Advanced Control Systems: More sophisticated systems that include automation, wireless controls, or customized safety features may add $10,000 to $50,000 or more to the cost, depending on the level of technology and customization required.
5. Maintenance and Operating Costs
The initial purchase and installation of the overhead crane are only part of the total cost. Ongoing maintenance and operational expenses are also important to consider when budgeting.
Preventative Maintenance: Regular maintenance is essential to keep the crane in safe working condition and prevent costly downtime. Annual maintenance costs can range from $2,000 to $10,000, depending on the size and complexity of the crane.
Energy Consumption: Overhead cranes consume energy, especially those that operate frequently or handle heavy loads. The energy costs will depend on the crane’s motor size and how often it is used. Energy-efficient cranes may have a higher initial cost but will save on electricity bills over time.
Spare Parts: Budget for the cost of spare parts, such as cables, hooks, and motors, which may need to be replaced periodically. Plan for an annual budget of $1,000 to $5,000 for parts replacement.
6. Training and Certification
Operator training is essential for the safe and efficient use of an overhead crane. Training costs can range from $500 to $5,000, depending on the level of training required and the number of operators being trained. Additionally, some regions may require certification for crane operators, which may add to the cost.
7. Insurance and Liability
Finally, you’ll need to consider the cost of insuring your overhead crane. Insurance premiums vary depending on the value of the crane and the level of coverage required. A typical insurance policy for an overhead crane may cost between $1,000 and $5,000 annually. Additionally, maintaining the crane to meet safety standards will help reduce potential liability and insurance costs.
Conclusion
Budgeting for an overhead crane in your factory requires careful consideration of multiple factors, including the type of crane, load capacity, installation, control systems, maintenance, and operational costs. By thoroughly evaluating these costs, you can ensure that you make a wise investment that enhances your factory’s productivity while keeping long-term expenses manageable. With a well-planned budget, you’ll be able to select the right overhead crane solution that fits your specific operational needs and financial constraints.
Comments