Lifting Challenges in Shipbuilding Solved with Double Girder Gantry Cranes
- blog@ellsenbridgecrane.com
- Jul 3
- 5 min read
The shipbuilding industry is one of the most demanding sectors in terms of material handling and lifting operations. From maneuvering massive steel plates and hull sections to positioning engines, propellers, and superstructures, the lifting requirements in a shipyard are unlike any other. To meet these challenges, shipyards worldwide rely on robust and precise lifting equipment. Among the most effective solutions are double girder gantry cranes-a vital piece of equipment engineered to handle the scale, weight, and complexity of shipbuilding processes.
In this article, we’ll explore the specific lifting challenges faced in shipbuilding and how double girder gantry cranes solve them through strength, stability, adaptability, and precision.

Common Lifting Challenges in Shipbuilding
1. Heavy and Oversized Loads Ship components such as hull blocks, deck modules, and propulsion systems are extremely large and heavy—sometimes weighing hundreds of tons. Transporting and positioning these components requires cranes that can handle extremely high loads without compromising stability or safety.
2. Precise Placement Requirements Ship construction demands accurate placement of each component to ensure structural integrity and alignment. Even minor misplacements can lead to costly rework or delays in the build schedule.
3. Variable Load Dimensions and Shapes Unlike standardized cargo containers or bulk goods, shipbuilding components come in irregular shapes and sizes. This irregularity adds to the difficulty of securing and maneuvering them safely.
4. Harsh Operating Environments Shipyards are typically located in coastal regions, where cranes must operate in open environments, exposed to humidity, salt spray, wind, and temperature variations. This demands high durability and corrosion-resistant materials.
5. Workflow Coordination Multiple lifting operations often occur simultaneously within a shipyard. Efficient coordination of these activities is essential to avoid bottlenecks and ensure smooth production flow.
6. Space Constraints and Yard Layout Modern shipyards are tightly packed, with limited space for assembly and material movement. Cranes must operate efficiently within these confined spaces without disrupting other operations.
How Double Girder Gantry Cranes Address These Challenges
1. High Load Capacity and Stability Double girder gantry cranes feature two parallel girders supported by end trucks running on rails or wheels. This configuration offers superior load-bearing capabilities compared to single girder cranes. Typically, double girder gantry cranes can lift loads ranging from 50 tons to over 500 tons, depending on customization.
This high capacity allows the safe and efficient handling of large ship modules, heavy machinery, and other substantial components essential to shipbuilding. The robust design ensures minimal deflection of girders even under full load, which contributes to long-term structural integrity and consistent performance.
2. Wide Span and High Lifting Height These cranes are engineered with customizable spans and lifting heights to accommodate the large dimensions of ship sections. A wide span enables the crane to straddle entire assembly lines or dry docks, facilitating end-to-end material movement.
High lifting height is especially critical for installing tall ship structures like masts or bridge modules. Double girder gantry cranes can be designed with the vertical reach necessary to lift and lower components into the required positions precisely.
3. Precision Control Systems Modern double girder gantry cranes are equipped with advanced control systems such as frequency inverters, programmable logic controllers (PLCs), anti-sway technology, and load monitoring systems. These features enable smooth and precise handling of delicate or awkwardly shaped loads.
Anti-sway systems, in particular, are indispensable in reducing load swinging during movement, which helps in placing large sections with pinpoint accuracy—essential for tasks like hull block assembly or engine installation.
4. Customizable Hoisting Mechanisms The hoisting mechanism in double girder gantry cranes is typically placed between the girders, allowing for optimal hook approach on all sides. These mechanisms can be customized with twin hoists for long loads or synchronized lifting when two cranes work together. This flexibility is crucial in shipyards where the load dimensions vary greatly between projects.
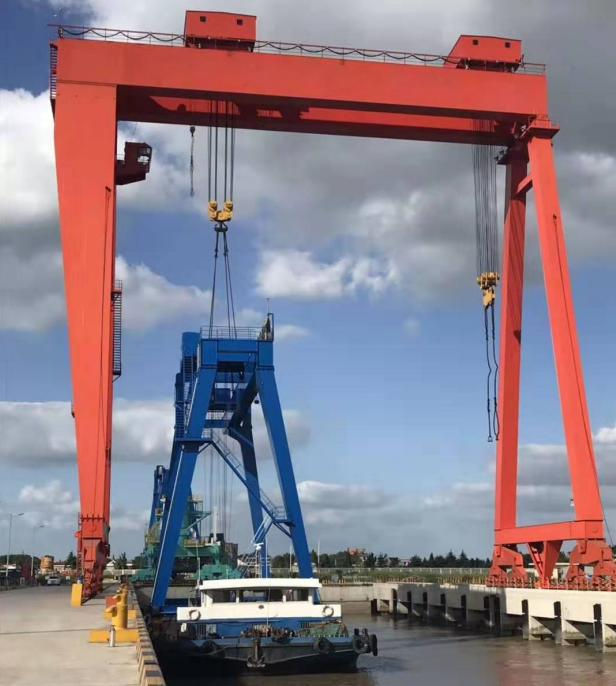
5. Corrosion-Resistant Construction for Marine Environments To cope with coastal weather conditions, double girder gantry cranes used in shipyards are manufactured with corrosion-resistant steel and treated with protective coatings. In some cases, stainless steel components or enclosed electrical systems are used to enhance durability and safety.
6. Integration with Shipyard Workflow These cranes are integrated into the broader shipyard logistics system. Some models can be equipped with automatic positioning systems, RFID tracking, and interfaces with yard management software to ensure that components are delivered and positioned in the right place at the right time.
By streamlining lifting and positioning tasks, double girder gantry cranes help reduce downtime, minimize manual intervention, and optimize production schedules.
7. Adaptability to Yard Layouts Depending on the space and operational constraints, double girder gantry cranes can be designed as:
Full gantry cranes (with two legs running on ground rails),
Semi-gantry cranes (with one leg and one side supported on a runway),
Or mobile rubber tyre gantry cranes for flexible operations without fixed rail infrastructure.
This adaptability makes it possible to tailor crane solutions to various shipyard layouts and production needs.
Real-World Applications in Shipbuilding
Many major shipyards around the world use double girder gantry cranes for critical stages of ship construction, including:
Hull Block Assembly: Lifting and aligning pre-fabricated blocks to form the ship’s hull.
Engine Installation: Hoisting massive marine engines into the engine room through tight vertical shafts.
Deck Module Positioning: Accurately placing superstructure modules such as cabins, bridges, and control towers.
Ship Outfitting: Supporting the installation of large accessories and equipment during final assembly.
Launching and Dry Dock Maintenance: Handling large components and supplies during the vessel launch or dry dock maintenance stages.
Benefits for Shipbuilders
By solving lifting challenges with double girder gantry cranes, shipbuilders gain several operational advantages:
Increased Efficiency: Fast and reliable lifting reduces assembly time and accelerates delivery schedules.
Enhanced Safety: Precision handling and anti-sway systems improve workplace safety for personnel and equipment.
Improved Quality: Accurate placement leads to better build alignment and fewer defects or rework.
Long-Term Cost Savings: Durable design and reduced downtime contribute to a lower total cost of ownership.
Scalability: Cranes can be scaled or upgraded as production volume and ship sizes increase.
Conclusion
Double girder gantry cranes are essential to overcoming the unique lifting challenges of shipbuilding. Their ability to handle massive loads, span wide areas, offer high precision, and operate reliably in tough environments makes them a cornerstone of modern shipyard operations.
As shipbuilders continue to construct larger and more complex vessels, the role of heavy-duty gantry cranes will only become more critical. Investing in well-designed, technologically advanced double girder gantry cranes is not just a matter of operational convenience - it’s a strategic decision that enables competitiveness, safety, and long-term productivity in the shipbuilding industry.
Comments