The Importance of 100-Ton Overhead Crane Girder Design in Steel Mill Operations
- blog@ellsenbridgecrane.com
- Apr 15
- 5 min read
In the heavy-duty operations of steel mills, where precision and safety are paramount, overhead cranes play a vital role. These cranes are used to lift and transport heavy steel components, scrap metal, and finished products across various stages of the manufacturing process. A critical aspect of ensuring the efficiency and safety of these cranes is the design of the crane girders, especially in cranes with high lifting capacities such as 100-ton overhead cranes.
The crane girder, or bridge girder, is the primary structural component of the overhead crane, responsible for supporting the entire load during lifting operations. For a steel mill, where operations are typically fast-paced and involve heavy, bulky loads, the proper design and engineering of an overhead crane 100 ton girder are indispensable. This article explores why the design of the crane girder is crucial in steel mill operations, focusing on the strength, stability, efficiency, and safety of these high-capacity cranes.

1. Understanding the Role of the Crane Girder
The crane girder is a horizontal beam that spans the width of the overhead crane, connecting the two end trucks and supporting the trolley and hoisting mechanisms. It is the core element of the crane bridge, which is responsible for carrying the load and transferring the stress and forces during lifting operations to the supporting structure. The girder needs to be strong enough to handle the weight of the load as well as the dynamic forces generated during movement.
For a 100-ton overhead crane, this responsibility becomes even more critical. These cranes typically handle massive loads such as steel slabs, billets, and coils, and they often operate in environments with extreme temperatures, high humidity, and continuous heavy-duty usage. The design of the crane girder directly affects the crane's performance, longevity, and safety.
2. Design Considerations for Strength and Load-Bearing Capacity
When designing a 100-ton overhead crane girder, one of the most critical factors is its ability to withstand the high weight loads and stress generated by lifting such heavy materials. The steel mill overhead crane will regularly encounter heavy and irregularly shaped loads, making it imperative that the girder is designed to maintain structural integrity under such extreme conditions.
Several key considerations influence the design to ensure strength and load-bearing capacity:
Material Selection: The girder is typically made of high-strength steel or steel alloys. These materials provide the necessary tensile strength and resistance to wear and tear, especially under the continuous heavy loads typical in steel mill operations.
Cross-Sectional Design: The cross-sectional shape of the girder plays a crucial role in load distribution. I-beam or box girder designs are commonly used for high-capacity cranes. These shapes help in maximizing load resistance while minimizing material weight.
Reinforcements: To enhance the load-bearing capacity, the girder may include reinforcements such as additional web plates, flanges, or ribs, which increase the strength of the girder without adding unnecessary weight.
Stress Distribution: The design of the crane girder must account for the stresses placed on it during operation. These stresses can vary depending on the type of load being lifted, the lifting speed, and the direction of movement. Engineers must use advanced structural analysis techniques to ensure the girder can evenly distribute the stress and avoid excessive deflection.
3. Stability and Structural Integrity
In steel mill operations, where cranes are constantly in use for various tasks, maintaining stability is a fundamental requirement. A 100-ton overhead crane must be designed to ensure stability during lifting, moving, and placing heavy materials without risk of buckling, swaying, or tipping.
Stability is primarily influenced by:
Girder Design and Alignment: The alignment of the girder with the rest of the crane structure must be precise. If the girder is misaligned, the entire crane system can become unstable, leading to uneven load distribution and a higher risk of accidents.
Load Swing and Anti-Sway Mechanisms: Heavy loads can cause the crane to sway as they are moved, creating instability. Anti-sway mechanisms, such as load positioners or sophisticated control systems, can help reduce swaying and improve the crane’s stability. The girder design should allow for the integration of such systems to enhance operational safety.
Deflection Limits: Even the smallest amount of deflection in the girder can have a significant impact on the crane's performance, leading to inaccuracies in load placement or increased wear and tear on the crane components. Designers must ensure the girder can withstand operational loads without excessive deflection, which could compromise stability and precision.
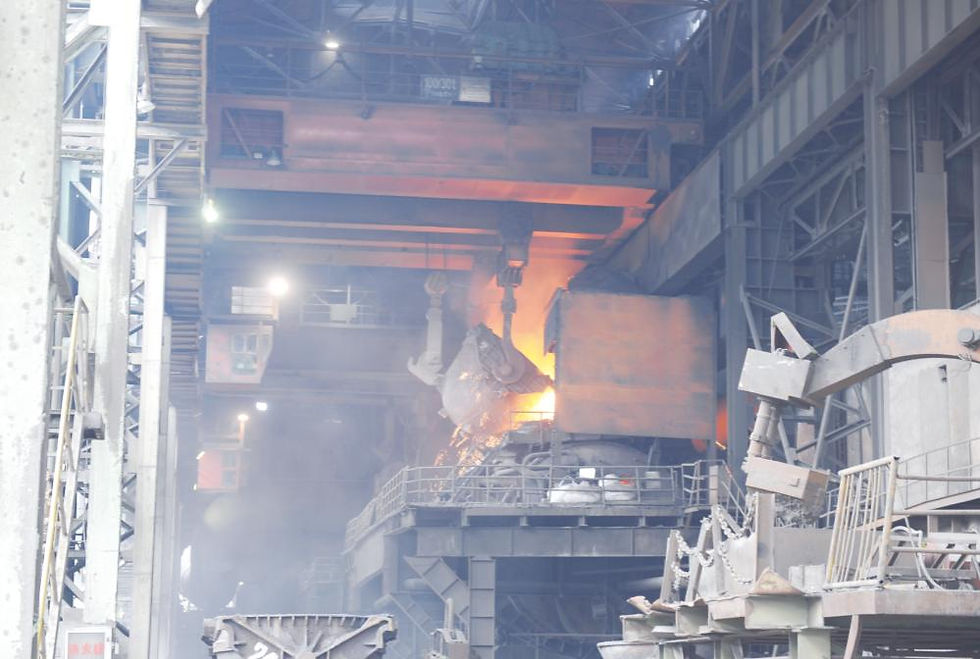
4. Efficiency and Operational Performance
Steel mills operate with tight schedules, and time efficiency is critical to maintain production goals. For a 100-ton overhead crane, efficiency is closely linked to the girder's design. A well-designed crane girder can ensure smooth and precise lifting operations, reduce the time spent on load positioning, and minimize downtime for maintenance.
The efficiency of the crane system is influenced by:
Speed and Smoothness of Operation: A properly engineered girder ensures that the crane can move heavy loads quickly and smoothly across the mill without delays or jerking movements. This is particularly important in steel mills, where time-sensitive tasks like material handling and transfer must be completed quickly.
Load Distribution and Reduction of Wear and Tear: The load must be evenly distributed across the girder to avoid concentrated stress points that could cause premature wear. Efficient designs also reduce the load on the wheels and rail systems, minimizing maintenance costs and prolonging the life of the entire crane system.
Energy Efficiency: Overhead cranes that require less energy to operate reduce operational costs for steel mills. Efficient girder designs help in reducing unnecessary friction or energy losses, improving the overall energy efficiency of the system.
5. Safety Considerations
Safety is paramount in any industrial setting, and steel mills are no exception. The proper design of a 100-ton crane girder is essential for preventing accidents, injuries, and damage to both workers and equipment. A poorly designed girder can lead to catastrophic failures during crane operations.
Key safety factors include:
Overload Protection: The crane girder must be designed to include mechanisms for overload protection, such as limit switches or automatic shutoffs. These systems prevent the crane from operating beyond its load capacity, ensuring that the girder overhead crane is not subjected to stresses that could cause structural failure.
Redundancy in Design: A redundant design ensures that if one component of the girder fails, the system can still function safely until repairs are made. This is critical in preventing accidents during heavy-duty operations in a steel mill.
Shock Absorption: During lifting, loads can generate shock loads that may exceed the typical stress limits of the girder. Incorporating shock absorbers or dampening systems into the crane girder design helps absorb these forces, reducing the impact on the crane structure.
6. Long-Term Durability and Maintenance
The lifespan of a 100-ton overhead crane depends heavily on the girder's design and the materials used. Steel mills require cranes that can operate under extreme conditions for many years without the need for constant repairs. The crane girder must be designed to withstand the harsh working environment of a steel mill, including high temperatures, corrosive environments, and heavy-duty usage.
A durable girder design minimizes maintenance needs and downtime, ensuring the crane operates reliably for the long term. Regular inspection and maintenance schedules should be based on the design of the girder and the load types it will encounter.
Conclusion
The design of a 100-ton overhead crane girder is crucial in steel mill operations, as it directly influences the crane's strength, stability, efficiency, safety, and durability. Given the demanding nature of steel mill environments, a properly designed girder ensures that the crane can handle heavy loads without compromising performance or safety. It is the cornerstone of safe and efficient steel mill operations, ensuring that cranes can function reliably for years while maintaining the high standards required in the steel industry.
Comments