Understanding the Trolley Mechanism of a Double Girder Bridge Crane
- blog@ellsenbridgecrane.com
- Jun 18, 2024
- 4 min read
Double girder bridge cranes are integral to many industrial settings, facilitating the lifting and transportation of heavy loads with precision and efficiency. Central to their functionality is the trolley mechanism, which ensures smooth and controlled movement of loads along the bridge girders. This article delves into the workings of the trolley mechanism, exploring its components, operation, and importance in industrial applications.
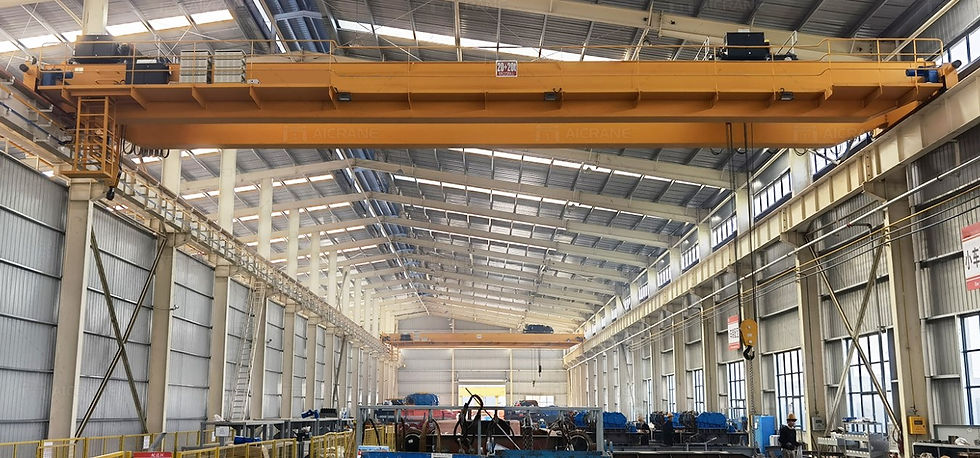
Components of the Trolley Mechanism
The trolley mechanism of a double girder bridge crane comprises several critical components, each playing a vital role in its overall functionality. These components include:
Trolley Frame: The structural foundation of the trolley, usually made from high-strength steel, ensuring durability and stability. It houses the other components and provides a stable platform for movement along the bridge girders.
Wheels and Rail System: The trolley moves along rails mounted on the top of the bridge girders. The wheels, typically made of hardened steel, are designed to reduce friction and wear, ensuring smooth travel along the rails.
Hoist: The hoist is responsible for the lifting and lowering of loads. It is mounted on the trolley frame and consists of a drum, wire rope or chain, motor, and a braking system. The hoist can be electrically or manually operated, depending on the crane’s design and application.
Motors and Drives: Electric motors drive the trolley wheels, providing the necessary force to move the trolley along the bridge girders. Variable frequency drives (VFDs) are often used to control the speed and acceleration of the trolley, enhancing precision and reducing mechanical stress.
Control Systems: Modern trolleys are equipped with advanced control systems that allow operators to maneuver the crane with high precision. These systems include joysticks, push-button pendants, or wireless remote controls, often integrated with programmable logic controllers (PLCs) for automated operations.
Safety Mechanisms: Safety is paramount in crane operations. The trolley mechanism is equipped with various safety features, such as limit switches, overload sensors, and emergency stop buttons, to prevent accidents and ensure safe operation.
Operation of the Trolley Mechanism
The operation of the trolley mechanism in a double girder bridge crane involves coordinated movements and precise control to ensure efficient load handling. The process can be broken down into several key steps:
Initiation: The operator initiates the movement through a control interface, selecting the desired direction and speed. This input is processed by the control system, which activates the appropriate motors and drives.
Movement Along Girders: The motors drive the trolley wheels, propelling the trolley along the rails mounted on the bridge girders. VFDs adjust the speed and acceleration, allowing for smooth starts and stops. The control system ensures that the trolley moves in the desired direction, maintaining stability and balance.
Lifting and Lowering Loads: The hoist mechanism, integrated into the trolley, handles the lifting and lowering of loads. The hoist motor, controlled by the operator, winds or unwinds the wire rope or chain on the drum, raising or lowering the load. The braking system ensures that the load remains stationary when needed, preventing unintended movements.
Positioning and Precision: Precise positioning is crucial for efficient operations. The control system, often aided by sensors and encoders, ensures that the trolley and hoist move to the exact desired location. This precision is vital for tasks that require accurate placement of heavy or delicate loads.
Safety and Monitoring: Throughout the operation, the trolley mechanism's safety features are active. Limit switches prevent the trolley from exceeding the designated travel range, while overload sensors monitor the weight of the load, ensuring it does not exceed the crane’s capacity. Emergency stop buttons allow the operator to halt all movements immediately in case of a malfunction or hazardous situation.
Importance in Industrial Applications
The trolley mechanism of a double girder bridge crane is crucial in various industrial applications due to its reliability, efficiency, and versatility. Some of the key benefits include:
Heavy Load Handling: Double girder bridge cranes, equipped with robust trolley mechanisms, can handle extremely heavy loads, making them indispensable in industries such as steel manufacturing, shipbuilding, and construction.
Precision and Control: Advanced control systems allow for precise positioning and smooth movement, essential for tasks that require high accuracy. This is particularly important in assembly lines, where components must be placed with exact precision.
Safety: The integration of safety features ensures that operations are conducted without accidents, protecting both the workforce and the equipment. This is critical in environments where safety is a top priority.
Efficiency: The ability to move heavy loads quickly and efficiently reduces downtime and increases productivity. The trolley mechanism’s smooth operation minimizes wear and tear, extending the lifespan of the crane and reducing maintenance costs.
Versatility: Double girder bridge cranes with trolley mechanisms are versatile, capable of handling various types of loads and accommodating different operational requirements. This adaptability makes them suitable for a wide range of industrial applications.
Conclusion
The trolley mechanism of a double girder bridge crane is a sophisticated system designed to ensure efficient, precise, and safe load handling in industrial environments. Its components, including the trolley frame, wheels, hoist, motors, control systems, and safety features, work in unison to provide reliable performance. Understanding the workings of this mechanism is essential for operators and engineers, ensuring optimal use and maintenance of the crane, thereby enhancing productivity and safety in industrial operations.
Comments