Load Distribution in the Structure of Rubber Tyred Gantry Cranes
- blog@ellsenbridgecrane.com
- Feb 19
- 5 min read
Rubber tyred gantry (RTG) cranes are essential pieces of equipment used primarily in container ports and freight yards to move and stack containers efficiently. The design and structure of these cranes must support substantial loads while maintaining stability and safety throughout their operations. One of the most critical factors in RTG crane performance is load distribution—how the weight of the container, the crane itself, and any additional dynamic forces during operation are distributed across various structural components.
This article will explore how load distribution works in the structures of rubber tired gantry cranes, the factors influencing it, and the importance of effective load management for crane performance, longevity, and safety.
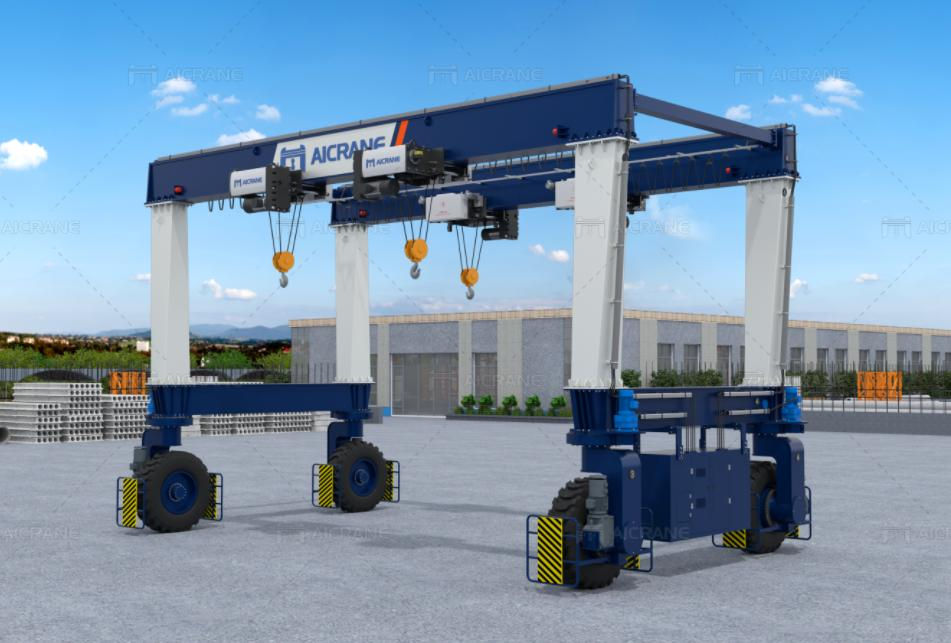
The Basic Structure of an RTG Crane
Before delving into load distribution, it’s essential to understand the basic components of an RTG crane. An RTG crane typically comprises:
The Gantry (Main Frame): This is the upper framework of the crane, consisting of the gantry legs, crossbeams, and the trolley rail system. The gantry serves as the primary support structure for the crane, ensuring it can lift and move heavy loads across its span.
The Trolley and Hoisting Mechanism: The trolley carries the hoist and lifting system, which raises and lowers the container. It travels along the rails on the gantry to position the load correctly.
The Tires (Rubber Tyres): RTG cranes are mounted on a set of rubber tyres, providing mobility across the yard. The tyres distribute the crane’s weight across the ground and allow it to move along a set path, typically designed for container stacking and handling.
The Operator’s Cabin: Situated on the gantry, the cabin houses the operator controls and monitoring equipment for crane operation.
The Lifting Hook: This is the part of the crane responsible for lifting the container. It is connected to the hoisting mechanism via cables or chains.
The efficiency of an RTG crane depends significantly on how well the loads are distributed across these structural components. Improper load distribution can lead to uneven wear, increased risk of tipping, and inefficient operations, ultimately reducing the crane's lifespan.
Factors Affecting Load Distribution in RTG Cranes
Several factors influence load distribution in RTG cranes. These include the weight of the load being lifted, the design of the crane, the movement of the crane during operation, and the terrain on which the crane operates.
The Weight of the Load: The primary concern for load distribution is the weight of the container being lifted. Typically, RTG cranes handle loads ranging from 20 tons to 40 tons per container. The crane’s ability to distribute this weight effectively across its structure is vital for operational safety and efficiency.
Center of Gravity (CG): The distribution of the weight in relation to the crane’s structure is crucial. The center of gravity of both the load and the crane needs to be kept within a stable zone, ensuring the crane remains balanced and does not tip during lifting operations.
Structural Design and Load Paths: The design of the RTG crane dictates how the load is transferred from the lifted container to the wheels supporting the crane. Ideally, the load should be evenly distributed across the gantry frame and tyres. To achieve this, engineers carefully design the gantry frame with specific load paths that help to spread the forces evenly throughout the structure.
Gantry Legs and Crossbeams: The gantry legs and crossbeams support the crane’s weight and distribute forces. These components are designed to absorb and transfer loads efficiently. The alignment of the legs with the tires is especially important in preventing localized stress on any one part of the crane.
Load Distribution from Hoisting Mechanism: As the hoist lifts a container, the load is transmitted through the hoisting ropes and into the trolley system. This force is then transferred into the gantry framework. If the hoist is not aligned properly, or if the trolley is too heavy, the load can shift in unexpected ways, leading to poor load distribution.
Tyre Load Distribution: RTG cranes rely on rubber tyres for mobility, and these tyres carry the entire weight of the crane and its load. The distribution of weight across the tyres affects how the mobile gantry crane moves and the efficiency of its operation.
Wheelbase and Tire Configuration: The length of the crane’s wheelbase and the number of tyres play a major role in distributing the crane’s weight. A longer wheelbase helps to distribute the load more evenly, reducing the risk of overloading individual tyres. The design and number of tyres are also critical in ensuring that the load is spread evenly across the ground, reducing wear on the tyres and minimizing the risk of crane instability.
Dynamic Forces and Load Shifting: During crane operation, various dynamic forces are introduced, such as acceleration, deceleration, and sway, all of which affect load distribution.
Swaying of the Load: The load’s natural sway (pendulum effect) can change the direction and magnitude of the forces acting on the crane. Load sway can create uneven stresses on the crane’s structure, potentially leading to instability. To counteract this, RTG cranes are often equipped with anti-sway systems to stabilize the load during movement.
Maneuvering Forces: As the crane moves to position itself under a container, additional forces are exerted on the crane structure. These forces impact load distribution, especially when moving on uneven surfaces. Uneven or poorly maintained yard surfaces can cause the crane to experience uneven weight distribution, leading to stress on the tyres and frame.
Environmental Conditions: The surface on which the crane operates can affect load distribution. Soft or uneven ground can result in the load being unevenly distributed, putting stress on the tyres and the gantry structure. In contrast, hard, level surfaces can improve load distribution and crane stability.
RTG Crane
Importance of Proper Load Distribution
Proper load distribution is crucial for several reasons:
Preventing Crane Tipping: If the load is not evenly distributed across the crane, there is a risk of the crane tipping over. RTG cranes are typically designed with a high degree of stability, but improper load distribution, especially in windy or dynamic conditions, can jeopardize safety.
Enhancing Efficiency: A well-balanced RTG crane performs more efficiently. When the load is distributed evenly, the crane can lift and move containers with greater precision and speed. Uneven distribution may result in delayed operation or reduced capacity.
Extending the Lifespan of the Crane: Proper load distribution helps minimize wear and tear on individual crane components, including tyres, tyres’ suspension system, hoisting mechanisms, and structural supports. This reduces the likelihood of premature failure, thus extending the crane’s operational lifespan.
Improving Safety: Proper load distribution contributes to overall safety, reducing the likelihood of accidents and minimizing wear on components that could lead to mechanical failure.
Conclusion
Load distribution in the structure of rubber tyred gantry cranes is a critical consideration that influences the crane's performance, efficiency, and safety. Engineers must carefully design these cranes to ensure that the load is evenly distributed across the gantry frame, tyres, and other structural components, taking into account dynamic forces, environmental conditions, and the characteristics of the load being handled.
By maintaining an optimal load distribution system, RTG cranes can operate safely and efficiently, reducing wear, increasing operational longevity, and improving productivity in container ports and freight yards worldwide.
Comments