The Role and Significance of Spreaders in RMG Container Cranes
- blog@ellsenbridgecrane.com
- Jun 23, 2024
- 4 min read
Rail Mounted Gantry (RMG) container cranes play a pivotal role in the efficient handling and transportation of shipping containers in port and intermodal terminals. Among the critical components of RMG cranes, spreaders stand out for their unique functionality and essential contribution to operational efficiency. This article delves into the four key aspects of spreaders in RMG container cranes: their design and structure, technological advancements, operational efficiency, and safety features.
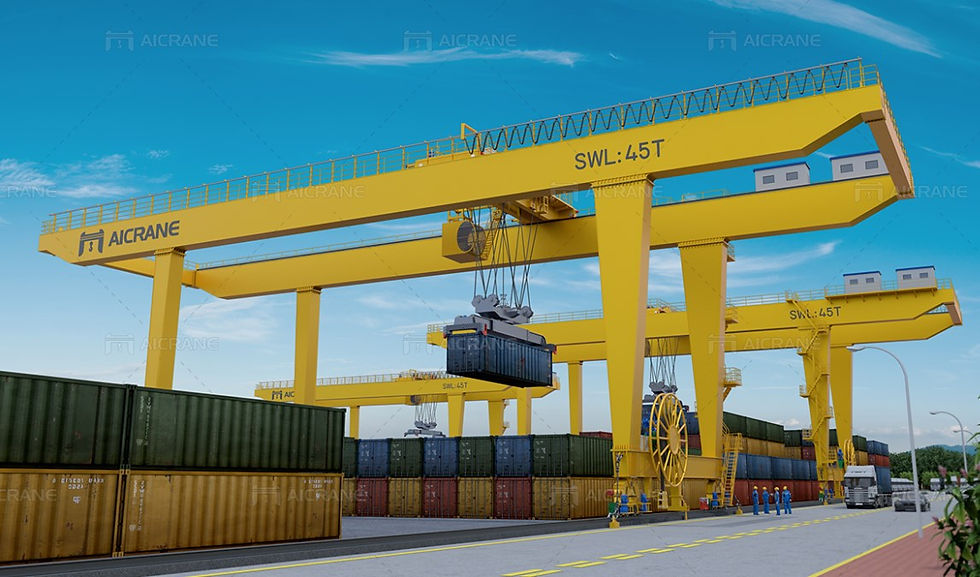
1. Design and Structure
Spreaders are the interface between the RMG crane and the container, designed to securely lift and transport containers of various sizes and weights. The design of a spreader is influenced by several factors, including the types of containers it handles, the operational environment, and the specific needs of the terminal.
A standard spreader has a rectangular frame with twist locks at each corner, which engage with the container’s corner castings to secure it during lifting. The spreader can adjust its size to accommodate different container lengths, typically ranging from 20 feet to 45 feet. This adjustability is achieved through telescopic mechanisms that allow the spreader to extend or retract as needed.
Materials used in the construction of spreaders are chosen for their strength and durability. High-tensile steel and advanced composites are commonly used to ensure that the spreader can withstand the stresses of lifting heavy containers repeatedly over long periods. Additionally, the spreader’s design must allow for easy maintenance and quick replacement of components to minimize downtime.
2. Technological Advancements
Modern spreaders incorporate various technological advancements to enhance their functionality and efficiency. One of the most significant innovations is the automation of the spreader adjustment process. Automated spreaders can change their configuration to match container sizes without manual intervention, significantly speeding up operations and reducing the risk of human error.
Another critical advancement is the integration of sensors and communication systems. Spreaders equipped with sensors can monitor parameters such as load weight, position, and alignment, providing real-time data to the crane operator. This information helps in making precise adjustments, ensuring the container is lifted safely and efficiently.
Additionally, the implementation of smart spreaders, which utilize Internet of Things (IoT) technology, allows for remote monitoring and diagnostics. These spreaders can communicate with central control systems, enabling predictive maintenance and reducing the likelihood of unexpected breakdowns. Smart spreaders also contribute to improved inventory management by providing accurate data on container movements.
3. Operational Efficiency
The efficiency of container handling operations is heavily influenced by the performance of spreaders. Efficient spreaders minimize the time taken to secure and lift containers, directly impacting the overall throughput of the terminal.
The speed and precision with which a spreader can engage and disengage with containers are critical factors in operational efficiency. High-performance spreaders can rapidly lock onto containers and release them, reducing cycle times and increasing the number of containers handled per hour. This efficiency is particularly important in busy ports where high throughput is essential to maintaining smooth operations.
The versatility of spreaders also contributes to operational efficiency. Spreaders that can handle multiple container sizes without requiring manual adjustment allow for more flexible and streamlined operations. This flexibility is crucial in environments where containers of varying sizes and types need to be handled continuously.
Moreover, spreaders designed for dual or tandem lifting, where two containers are lifted simultaneously, can significantly boost productivity. These advanced spreaders require precise synchronization and robust design to handle the increased load and complexity, but they offer substantial gains in handling capacity.
4. Safety Features
Safety is a paramount concern in container handling operations, and spreaders are equipped with numerous safety features to protect both personnel and equipment. One of the primary safety mechanisms is the twist lock system, which ensures that containers are securely attached to the spreader before lifting. Modern twist locks are often automated and include sensors that confirm proper engagement before lifting operations commence.
Anti-sway systems are another critical safety feature. These systems stabilize the spreader and the container during lifting and movement, reducing the risk of accidents caused by swinging loads. Advanced spreaders may also include load-sensing technology that monitors the weight and distribution of the load, preventing overloading and ensuring safe lifting practices.
Emergency stop mechanisms are integrated into spreaders to allow immediate cessation of operations in the event of a malfunction or hazard. These mechanisms can be activated manually by the operator or automatically by the control system in response to detected anomalies.
Additionally, spreaders are designed with ergonomic considerations to protect operators from strain and injury. Controls are positioned for easy access, and automated systems reduce the need for manual intervention, minimizing the physical demands on operators.
Conclusion
Spreaders are a critical component of RMG container cranes, contributing significantly to the efficiency, safety, and technological advancement of container handling operations. Their design and structure ensure robust performance, while technological innovations enhance operational efficiency and safety. By incorporating advanced materials, automation, and smart technologies, modern spreaders meet the evolving demands of high-capacity ports and intermodal terminals, underscoring their indispensable role in the logistics and transportation industry.
Comments