The Role of Anti-Collision Systems in Rubber Tired Gantry Crane Operations
- blog@ellsenbridgecrane.com
- Apr 4
- 6 min read
In the world of port operations, where heavy-duty equipment plays a pivotal role in the smooth movement of containers, safety is paramount. Among the numerous pieces of equipment used in container terminals, the Rubber Tired Gantry (RTG) crane is one of the most essential. RTG cranes are designed for handling containers in yards, where their ability to move freely across the storage area offers significant advantages. However, with the complexity of operations, particularly in busy and congested environments, the risk of collisions becomes a critical concern. This is where anti-collision systems play a key role, ensuring both operational efficiency and safety.

Understanding Rubber Tired Gantry Cranes
Before diving into the specifics of anti-collision systems, it's important to understand the operation of a rubber tired gantry crane. Rubber Tired Gantry cranes are mobile container cranes that use rubber tires for mobility, allowing them to traverse the container yard. These cranes are primarily designed for lifting, stacking, and transporting containers. Their ability to move horizontally and vertically makes them highly versatile in container terminals, where efficient space utilization and fast turnaround times are crucial.
RTG cranes typically operate in environments where numerous cranes are working simultaneously, often in tight spaces. These cranes are used to stack containers, load and unload ships, and transport cargo across large yards. The fact that they move along designated routes and interact with various pieces of equipment, such as straddle carriers, reach stackers, and other RTGs, increases the likelihood of potential collisions. Therefore, it’s imperative to integrate systems that prevent accidents and enhance operational safety.
The Need for Anti-Collision Systems
The introduction of anti-collision systems into RTG crane operations is primarily driven by safety concerns. Collisions between cranes, containers, or other vehicles can cause significant damage to both the equipment and the cargo, leading to costly repairs and delays. More importantly, they pose a serious risk to workers operating in these areas. In container terminals where high-efficiency levels are required, the frequency of crane movements and the size of the equipment make collisions an ever-present risk. As these cranes handle cargo weighing several tons, even a minor collision can result in catastrophic consequences.
Additionally, congestion within container yards, high-speed crane movements, and the potential for human error contribute to the risks. Crane operators may struggle to navigate through the complex layout of the yard, and manual monitoring of all potential collisions may not be feasible. Therefore, an automated and reliable anti-collision system is essential to prevent accidents and improve safety in these busy environments.
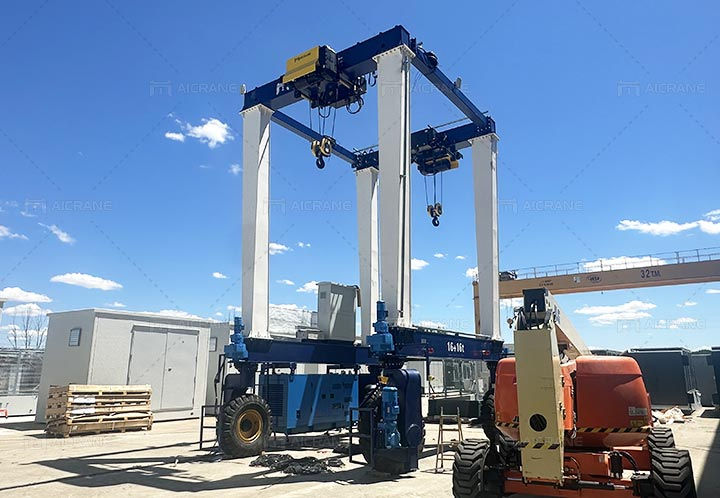
How Anti-Collision Systems Work
Anti-collision systems in RTG cranes utilize a combination of sensors, cameras, and advanced software algorithms to detect and prevent potential collisions. The systems monitor the position and movement of the crane, the surroundings, and any obstacles that might come into its path. Here's how they typically function:
Sensor Technology: Anti-collision systems are equipped with various sensors, including proximity sensors, radar, ultrasonic sensors, and laser scanners. These sensors are strategically placed on the crane to monitor the area around it, particularly in the blind spots where the operator might not have full visibility. Radar and laser scanners are often used to detect objects in the crane’s path, such as containers, other cranes, or any obstacles on the ground.
Real-Time Data Processing: Once the sensors collect data, it is fed into an onboard computer system. This system processes the real-time information to identify any potential risks or hazards. The system is designed to compare the movement of the crane with predefined safe operating zones, ensuring that the crane operates within the designated path.
Warning Signals: If a potential collision is detected, the anti-collision system triggers a series of warning signals to alert the crane operator. These signals can take various forms, such as visual alarms, audio warnings, or flashing lights, indicating the presence of an obstacle or an impending risk. This allows the operator to take immediate action, such as slowing down or stopping the crane.
Automated Collision Prevention: In some advanced anti-collision systems, the technology can automatically intervene in the crane’s operation. The system may slow down or stop the crane to prevent a collision with another piece of equipment or an obstacle. In certain systems, the crane may even be programmed to reroute or adjust its path to avoid danger.
Communication Between Cranes: In more sophisticated anti-collision systems, cranes are equipped with a communication module that allows them to exchange information with each other. This is particularly useful in environments where multiple RTGs are operating simultaneously. If one crane is in danger of colliding with another, the system can inform both operators, preventing accidents. Such systems are often referred to as “inter-crane communication systems.”
Types of Anti-Collision Systems in RTG Cranes
There are several different types of anti-collision systems employed in RTG crane operations, each with its own set of features and advantages. Some of the most commonly used systems include:
Laser-based Systems: Laser scanners are highly effective in detecting objects and obstacles within the crane's path. These systems are particularly useful in environments with varying obstacles, such as containers and vehicles. Laser-based anti-collision systems work by emitting a laser beam that scans the environment, identifying any objects in the crane's vicinity.
Radar-based Systems: Radar sensors are another popular choice for detecting objects and measuring distances. Radar systems are known for their ability to detect objects at greater distances and under challenging weather conditions, such as fog, rain, or snow. They are often used in combination with other sensor types to enhance the overall accuracy of the system.
Proximity Detection Systems: These systems use proximity sensors that create a virtual “safe zone” around the gantry mobile crane. When an object enters this zone, the system issues an alarm or activates automatic braking to prevent a collision. Proximity detection systems are often used for detecting obstacles in close proximity to the crane, such as other equipment or pedestrians.
CCTV Systems: CCTV cameras provide visual monitoring of the surrounding area, giving the operator a clearer view of the environment around the crane. Some systems integrate video feeds with motion detection algorithms, allowing the crane to automatically stop or slow down if a person or object enters a restricted area.
GPS-based Systems: GPS technology is also utilized to track the precise location of cranes within a yard. This is particularly useful for preventing collisions between cranes, as the system can ensure that they maintain a safe distance from one another. GPS-based systems are often combined with other sensor technologies to create a comprehensive anti-collision solution.
Benefits of Anti-Collision Systems
The implementation of anti-collision systems in RTG crane operations offers numerous benefits, including:
Enhanced Safety: The primary advantage of anti-collision systems is their ability to improve safety in crane operations. By preventing accidents, these systems protect both operators and ground workers, reducing the risk of injury or fatalities.
Reduced Equipment Damage: By preventing collisions, anti-collision systems help protect cranes and other equipment from damage. This leads to fewer repairs, less downtime, and lower maintenance costs for terminal operators.
Improved Operational Efficiency: With the ability to reduce the likelihood of accidents and ensure smooth crane operations, anti-collision systems contribute to better operational efficiency. This is crucial in busy ports where maximizing throughput is key to profitability.
Compliance with Safety Regulations: Many countries have stringent safety regulations governing the operation of cranes and other heavy equipment. Anti-collision systems help ensure compliance with these regulations, avoiding fines and ensuring that operators meet safety standards.
Increased Reliability: The integration of these systems makes crane operations more reliable, ensuring minimal disruption and a safer work environment. This increases the confidence of employees and stakeholders in the operational safety of the terminal.
Conclusion
As port operations become increasingly complex, with higher demands for speed and efficiency, the importance of safety cannot be overstated. Anti-collision systems are a vital tool in ensuring that Rubber Tired Gantry cranes can operate efficiently without compromising safety. By reducing the risk of accidents, preventing damage to equipment and cargo, and providing enhanced operational reliability, these systems play a crucial role in modern port operations. As technology continues to advance, the future of RTG cranes will undoubtedly see even more sophisticated anti-collision systems that further improve the safety and efficiency of container handling worldwide.
Comments